Concrete is not only hard - but also soft when shaped by design
SINCE 2013
Sconcrete is a fiber concrete furniture manufacturing company founded in 2013, formerly an export handicraft and ceramics production facility. Focus on material purity and environmental sustainability, we strive to showcase the beauty of nature and the craftsmanship of the Vietnamese people to the world.
• 3,000 m2 production area
• Permanent workforce of 20+
• 5,000 items per month production capacity
• Supply worldwide to over 6 countries
• 10+ years of manufacturing experience in Vietnam
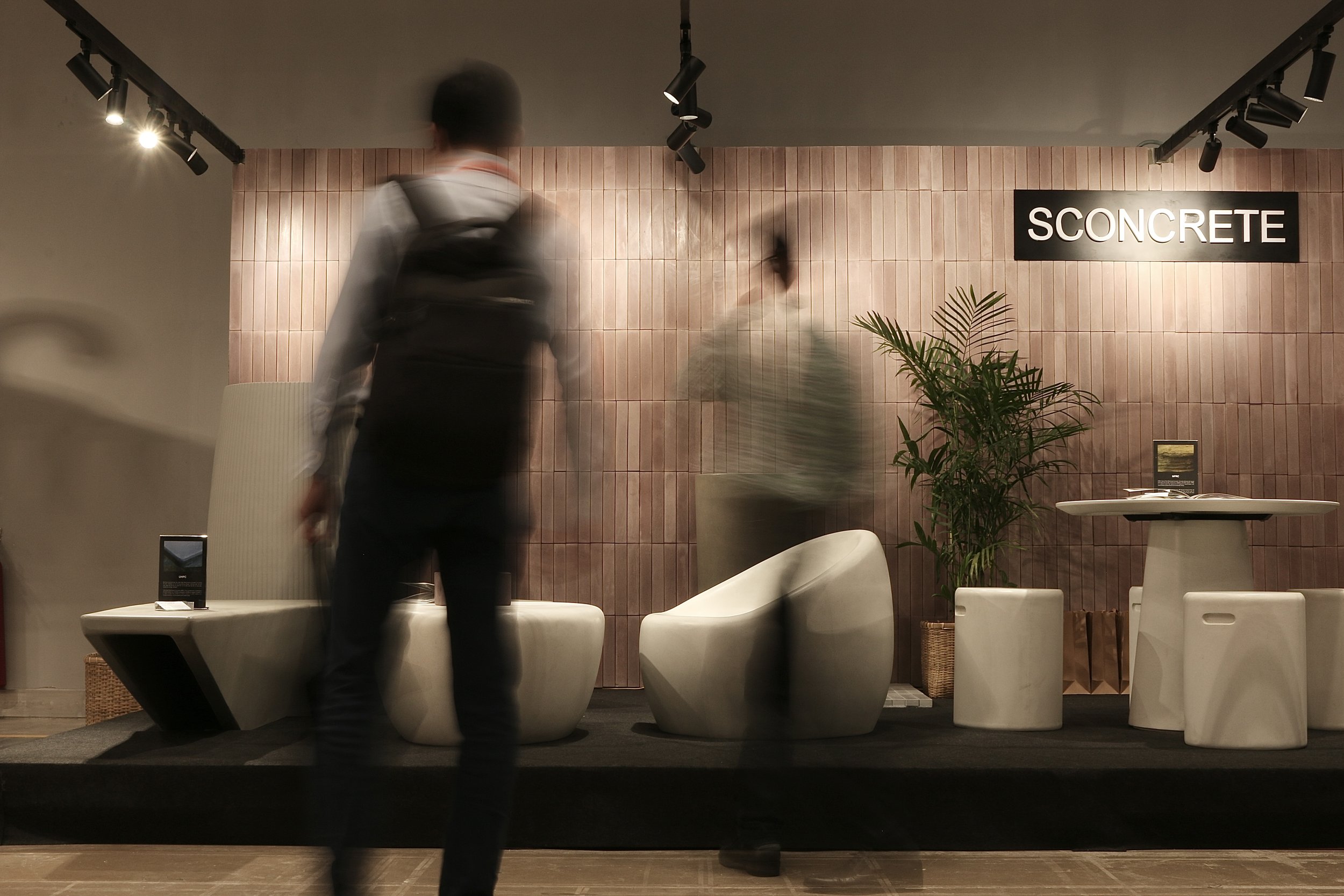
SCONCRETE VIBE 2024
KARA CREAM STONE
KARA ALBA WHITE
TURA D120 CREAM STONE
TURA D120 ALBA WHITE
MISSION
With a focus on material purity and environmental sustainability, we strive to showcase the beauty of nature and the craftsmanship of the Vietnamese people to the world. Backed by over 10 years of experience, Sconcrete is confident in its ability to satisfy even the most demanding customers.
OUR PARTNERS
WHAT WE MAKE
NFRC (Natural Fiber Reinforced Concrete): Concrete reinforced with natural plant fibers such as jute, coconut coir, seagrass, and water hyacinth | GFRC or GRC (Glass Fiber Reinforced Concrete): This is fiberglass-reinforced concrete. It is similar to NFRC but replaces cellulose plant fibers with fiberglass.
High-performance concrete (HPC), with a compressive strength of 60-70 MPa (compared to 30 MPa for regular concrete), is a cement mortar mixture with strictly controlled ingredients, including Portland cement, silica, additives, and more. It is used for products such as wall tiles, washbasins, and bathtubs.
Ultra High Performance Concrete (UHPC): This concrete has a compressive strength greater than 100 MPa (compared to 30 MPa for regular concrete). It is highly durable and suitable for outdoor projects in harsh weather and climate conditions, such as deserts and coastal areas.
PRODUCTION METHODS
1. Concept to Prototype
Depending on the requirements for accuracy or the tactile quality of the form, the prototype will be handcrafted in plaster or converted into a digital file and processed through a 3D printer.
2. Mold Crafting
Sconcrete use various materials to shape molds. For forms with high surface texture, elastic liquid materials are used to capture the structure and surface details.
3. Shell Removal
Once the mold structure has hardened, the outer shell is removed. The high elasticity of the shaping liquid allows for precise replication of the surface details of the original design prototype.
4. Demolding
The mold can be reused multiple times for production orders. The prototype will be kept confidential upon the customer's request.
5. Concrete Forming
The concrete mixture is applied into the mold either by hand-layering onto the mold surface or by liquid pouring. This process is carried out in the production workshop.
6. Demolding & Finishing
Once the concrete has hardened, the product is removed from the mold and undergoes surface finishing. The mold is then ready for reuse in step 5.